What Is PVD Coating vs. Vacuum Coating
Let’s kick things off with a common misconception—many people think PVD coating and vacuum coating are the same. While they both happen in a vacuum environment, they are far from identical. So, if you’ve ever wondered what separates these two processes, you’re in the right place.
In the world of manufacturing, surface enhancement plays a critical role. Whether it’s your smartphone’s sleek finish, a luxury watch’s glossy surface, or high-performance cutting tools, the coatings used can dramatically affect performance, durability, and aesthetics.
But not all coatings are created equal. PVD coating and vacuum coating are two standout methods that are often thrown into the same bucket. However, they are distinct both in their processes and outcomes.
Understanding the nuances between PVD and vacuum coating isn’t just for engineers or factory workers—anyone involved in design, product development, or even consumer electronics can benefit.
With advancements in nanotechnology and material science, these coatings are becoming increasingly important across a wide array of industries.
So buckle up. We’re diving deep into the world of coating technology—explaining everything from how each method works to where they’re most commonly used.
By the end, you’ll be well-versed in what makes PVD coating and vacuum coating unique and how to choose the right one for any application.
Table of Contents
What Is PVD Coating?
PVD stands for Physical Vapor Deposition. At its core, this is a vacuum deposition method used to produce thin films and coatings. In a nutshell, the process involves turning a solid material—usually a metal—into vapor, which then condenses onto the surface of the object being coated. But it’s not just as simple as “heat, vapor, deposit.”
PVD coating uses physical processes such as thermal evaporation, sputtering, or arc discharge to transfer material from a source to the target object. Unlike chemical methods (like CVD—Chemical Vapor Deposition), PVD doesn’t rely on chemical reactions. Instead, it’s purely a physical transformation that occurs under vacuum conditions.
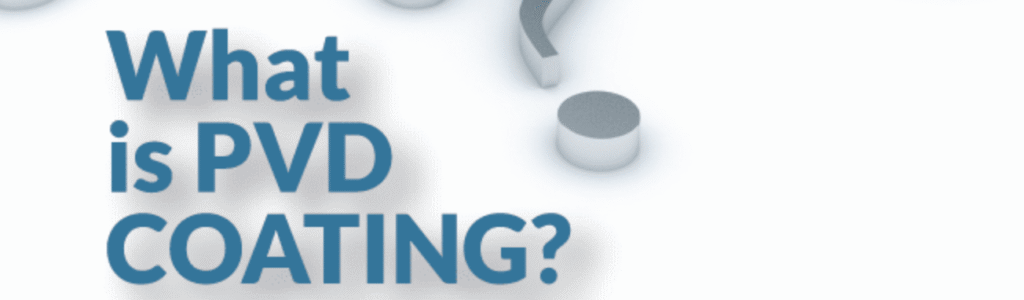
PVD has been around since the 19th century in one form or another, but it has seen significant advancements since the 1980s, thanks to developments in vacuum technology, materials science, and surface engineering. Today, it’s used in everything from aerospace components to biomedical tools and even fashion accessories like watches and jewelry.
One of the main appeals of PVD is its versatility. You can apply a range of metals—such as titanium, zirconium, aluminum, and chromium—to a wide variety of substrates, including metals, plastics, and glass. The end result? A super thin, super strong, and often super pretty coating that improves both function and form.
The Process Behind PVD Coating
Now let’s get into the nitty-gritty of how PVD actually works. This isn’t your average spray paint job—PVD involves advanced machinery and tightly controlled environments to ensure precision at the atomic level.
Step-by-Step Breakdown
- Preparation of Substrate: The object to be coated (also called the substrate) must be meticulously cleaned—often using ultrasonic cleaners and plasma etching—to ensure there’s no contamination. Even a speck of dust can ruin the entire process.
- Vacuum Creation: The coating chamber is sealed and pumped down to an ultra-high vacuum (UHV), usually below 10⁻⁵ torr. This ensures that the vaporized metal travels directly to the target without colliding with air molecules.
- Material Vaporization:
- In thermal evaporation, the metal is heated until it vaporizes.
- In sputtering, a high-voltage electric field bombards a metal target with ions, causing atoms to “sputter” off.
- In arc evaporation, a high-current, low-voltage arc creates localized spots that rapidly vaporize the metal.
- Deposition on Substrate: The vaporized atoms travel through the vacuum and condense on the cooler surface of the substrate, forming a thin, uniform coating layer.
- Cooling & Finishing: After deposition, the object is cooled and may undergo additional treatments like annealing or polishing, depending on the intended application.
PVD Equipment
You’ll find various types of machinery involved:
- Vacuum chambers
- Target holders
- Power supplies (for sputtering or arc)
- Rotating fixtures to ensure even coating
- Gas inlets (often for inert gases like argon)
Every step is finely tuned. Even minor variations in temperature, pressure, or gas flow can impact the coating’s quality and performance.
Applications of PVD Coating
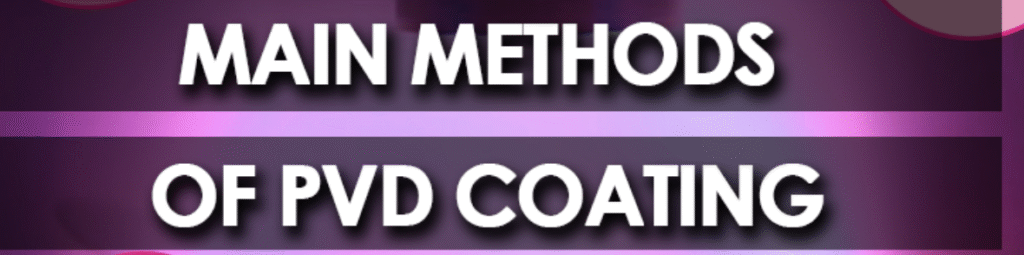
PVD coating isn’t just a fancy word used in aerospace labs—it’s everywhere, even in places you’d least expect.
1. Industrial Tools
Think drill bits, end mills, and cutting tools. PVD-coated tools last longer, cut cleaner, and resist heat better than uncoated ones. This translates to more efficient production lines and lower maintenance costs.
2. Automotive Industry
In the auto world, it’s all about performance and looks. PVD coatings are used on engine parts, piston rings, and decorative trim to enhance both durability and style.
3. Consumer Electronics
That sleek, smudge-resistant finish on your phone or laptop? That’s likely a PVD coating. It doesn’t just look good—it also protects against scratches and corrosion.
4. Medical Equipment
Surgical tools, implants, and even dental instruments benefit from PVD’s biocompatibility and corrosion resistance.
5. Watches and Jewelry
Gold, black, rose gold—those chic finishes on watches and rings? Yep, that’s PVD. It offers a luxe look without the high cost or fragility of pure metals.
6. Optics and Glass
Anti-reflective and mirror coatings on lenses are often done using PVD to ensure clarity and durability.
Bottom line? PVD is as versatile as duct tape but way more high-tech.
Advantages of PVD Coating
So, why go through all this trouble when other coating methods are out there? Because PVD has a serious edge, especially when it comes to performance and eco-friendliness.
1. Exceptional Hardness
PVD coatings like titanium nitride (TiN) can reach hardness levels up to 2500 HV (Vickers Hardness), making them ideal for high-wear environments.
2. Superior Adhesion
Since the vapor condenses directly onto the substrate, the coating forms a strong mechanical bond. This reduces the risk of peeling or chipping, even under stress.
3. Corrosion and Oxidation Resistance
Whether you’re dealing with salty seawater or reactive chemicals, PVD coatings offer a robust shield.
4. Environmentally Friendly
No hazardous chemicals, no toxic waste. PVD is a dry process, meaning fewer emissions and safer working conditions.
5. Aesthetic Flexibility
You can tailor the color, texture, and finish to suit different tastes and brand identities. From matte black to rainbow hues—it’s all possible.
6. Long-Term Cost Savings
While the upfront costs may be higher than traditional coatings, the durability and reduced maintenance often pay off in the long run.
fusion.
Vacuum coating encompasses multiple techniques, including:
- PVD (Physical Vapor Deposition)
- CVD (Chemical Vapor Deposition)
- Evaporation coating
- Sputter coating
Each method involves placing the substrate and the coating material inside a vacuum chamber. From there, the material is transferred onto the substrate, either through a physical or chemical process. The lack of air or gas in the chamber allows for a highly controlled environment, which leads to cleaner, more uniform coatings.
What Sets It Apart?
Unlike PVD, vacuum coating is not limited to physical methods. For instance, CVD uses chemical reactions between gases and the substrate to create the coating. These reactions often occur at higher temperatures and result in very dense and uniform films—ideal for semiconductors and high-precision components.
Additionally, vacuum coating can be used for a much wider range of film thicknesses and materials. While PVD generally deals with thin metallic films, vacuum coating can also include organic layers, dielectrics, and semiconductors.
The Process of Vacuum Coating
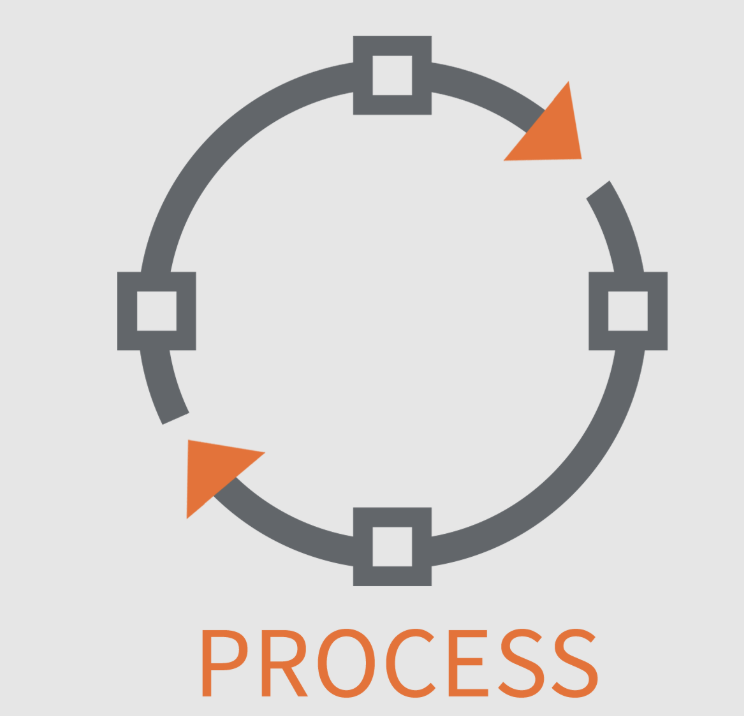
Let’s break down how vacuum coating works step by step. Though it varies slightly based on the specific technique used, the overarching workflow is fairly consistent.
1. Substrate Preparation
As with PVD, cleanliness is critical. The substrate is cleaned using solvents, ultrasonic baths, or plasma etching. Even microscopic debris can compromise the integrity of the final product.
2. Chamber Evacuation
The chamber is evacuated to remove air and moisture. This step ensures that no contaminants interfere with the deposition process. The vacuum levels here are similar to those in PVD, typically ranging between 10⁻⁴ and 10⁻⁸ torr.
3. Deposition
Here’s where things diverge based on the method:
- In evaporation coating, the material is heated until it vaporizes and condenses on the substrate.
- In sputtering, particles are ejected from a target and land on the surface.
- In CVD, reactive gases are introduced, and the coating forms via chemical reactions on the heated surface of the substrate.
4. Post-Processing
After deposition, the coated substrate may be cooled, annealed, or further treated to enhance properties like hardness, adhesion, or appearance.
Equipment Used
Vacuum coating setups include:
- High-vacuum chambers
- Power supplies
- Material sources (e.g., metal targets, chemical gas lines)
- Substrate holders with rotation or movement mechanisms
While the machinery may look similar to PVD equipment, the added complexity of chemical handling (especially in CVD) can make vacuum coating systems more intricate.
Applications of Vacuum Coating
Vacuum coatings are all around us. From your kitchen to outer space, the technology is used in hundreds of applications that enhance performance, durability, and aesthetics.
1. Optics and Glass
Vacuum coatings are widely used to make anti-reflective coatings, mirrors, and lens filters. Precision is key here, as the coatings must be perfectly uniform.
2. Solar Panels
Thin-film solar cells often rely on vacuum-deposited layers. These coatings help in improving light absorption and electrical conductivity.
3. Electronics
Printed circuit boards (PCBs), microchips, and displays all benefit from vacuum-deposited insulating or conductive layers.
4. Packaging
Yes, even potato chips! Some food packages are coated using vacuum processes to make them light-resistant and airtight.
5. Aerospace and Defense
Thermal control coatings, radar-absorbing materials, and specialized protective layers all come from the vacuum coating universe.
6. Decorative Finishes
Think metallic films on plastics, chrome-like finishes, and shiny decals. These are all achieved through various vacuum coating methods.
Vacuum coating’s versatility is what makes it so valuable—it can be adapted for both heavy-duty industrial tools and everyday consumer products.
Advantages of Vacuum Coating
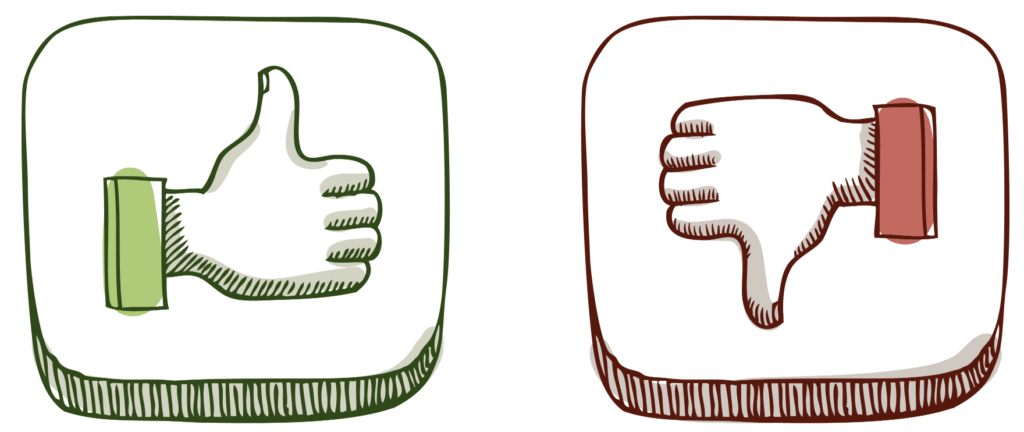
So, what makes vacuum coating such a powerhouse in modern manufacturing and design? The benefits go far beyond mere aesthetics.
1. High Purity Coatings
Thanks to the ultra-clean vacuum environment, the resulting films are free from contamination. This is especially important in medical and semiconductor industries.
2. Uniformity and Precision
Vacuum coating allows for a high degree of control over thickness and composition. This is critical in optics, electronics, and other precision-dependent fields.
3. Broad Material Compatibility
Whether you’re working with metals, ceramics, or polymers, vacuum coating has a solution. The techniques can be customized to suit nearly any substrate.
4. Enhanced Functional Properties
Coatings can improve electrical conductivity, thermal resistance, corrosion resistance, and even biocompatibility.
5. Scalability
Vacuum coating systems range from small research chambers to large-scale production lines. This flexibility allows it to be adopted in both R&D and mass manufacturing.
6. Reduced Environmental Impact
Like PVD, many vacuum coating methods (especially physical ones) are dry processes, meaning they produce little to no hazardous waste. Compared to traditional painting or plating, it’s a much greener option.
PVD Coating vs. Vacuum Coating: Key Differences
Let’s set the record straight: PVD is a type of vacuum coating, but the two are not interchangeable terms. Think of it like this—all golden retrievers are dogs, but not all dogs are golden retrievers.
Here’s a breakdown to clarify the differences:
Feature | PVD Coating | Vacuum Coating |
---|---|---|
Definition | A physical method to deposit material in a vacuum | An umbrella term including PVD, CVD, and more |
Process Type | Physical | Physical and/or Chemical |
Temperature | Generally lower (150–500°C) | Can be higher (especially CVD methods) |
Materials Used | Primarily metals | Metals, ceramics, polymers, etc. |
Precision | Very high | Varies depending on the method |
Applications | Tools, electronics, jewelry | Optics, solar panels, semiconductors |
In short, PVD is a subset of vacuum coating, optimized for thin, durable, high-performance films. Vacuum coating, on the other hand, is a broader category that offers more techniques and applications.
Disadvantages of PVD Coating
While PVD coating has plenty of perks, it’s not all sunshine and rainbows. There are certain drawbacks that might make it less ideal depending on your needs or setup.
1. High Initial Investment
One of the biggest hurdles in implementing PVD technology is the cost of equipment. Vacuum chambers, power supplies, and maintenance requirements can easily run into hundreds of thousands of dollars. This makes it less accessible for small-scale manufacturers or startups unless they outsource the process.
2. Limited Coating Thickness
PVD coatings are typically very thin—ranging from 0.1 to 5 microns. While this is perfect for applications like wear resistance or aesthetics, it might not be ideal where a thicker barrier layer is needed, such as heavy corrosion protection or insulation.
3. Surface Preparation Is Crucial
The success of a PVD coating is highly dependent on the cleanliness and smoothness of the substrate. Any imperfections, oils, or particles on the surface can lead to adhesion issues, pinholes, or weak spots in the coating. This adds extra labor and time for surface prep.
4. Line-of-Sight Limitation
In PVD, the vaporized material travels in straight lines. This means objects with complex geometries, like deep grooves or undercuts, may not get evenly coated. Extra tooling or repositioning may be required, complicating the process.
5. Limited to Vacuum-Compatible Materials
Certain materials that degrade or outgas under vacuum (like some plastics) are unsuitable for PVD unless pre-treated or specially prepared.
Despite these challenges, many companies still opt for PVD because the long-term benefits outweigh the limitations—especially in high-performance industries.
Disadvantages of Vacuum Coating
Just like PVD, vacuum coating has its own set of limitations. It’s powerful and flexible, but not always the perfect fit.
1. High Operational Complexity
Depending on the specific technique (CVD, sputtering, etc.), vacuum coating can require complex setups and highly skilled technicians. Managing the right vacuum levels, deposition rates, and chemical reactions takes experience and precision.
2. Time-Consuming Process
Vacuum coating cycles can be lengthy, especially for multi-layer coatings or those requiring high-purity results. Pumping the vacuum, prepping substrates, and conducting post-processing steps all add to the timeline.
3. Potential Hazardous Chemicals
In some types of vacuum coating like CVD, gases used may be toxic, corrosive, or flammable, demanding additional safety protocols and ventilation systems. This adds to the infrastructure and training costs.
4. Equipment Wear and Maintenance
Vacuum systems, especially those dealing with reactive gases or high temperatures, are prone to wear over time. Regular maintenance is necessary to prevent contamination, ensure consistent results, and prolong machine life.
5. Not Always Economical for Small Runs
Because of setup time and equipment requirements, vacuum coating is best suited for large-scale production. For smaller runs, the cost per unit might be too high to justify unless premium performance is absolutely required.
These disadvantages don’t negate vacuum coating’s value—they just highlight that it’s not a one-size-fits-all solution.
Choosing Between PVD and Other Vacuum Coating Methods
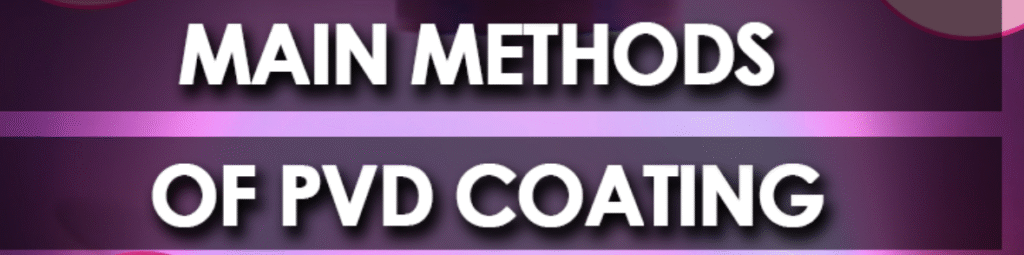
So how do you decide between PVD and another vacuum coating method like CVD or evaporation? It depends on several factors:
1. Desired Coating Properties
- Need high hardness and wear resistance? Go with PVD.
- Looking for thick, dense coatings? CVD might be better.
- Need ultra-thin, decorative coatings? Evaporation coating could be your pick.
2. Material Compatibility
Some substrates can’t withstand the high temperatures of CVD, making PVD or low-temperature vacuum evaporation more appropriate.
3. Part Geometry
If you’re coating parts with deep recesses or complex shapes, line-of-sight methods like PVD may fall short. In such cases, CVD, which can conform to surfaces more easily, may be the better choice.
4. Budget and Volume
- Small batch or prototype production? PVD offers lower contamination risk and easier switching between materials.
- High-volume, high-precision production? Vacuum coating systems with automated chambers and multi-process capabilities make sense.
5. Environmental Regulations
PVD and most vacuum evaporation processes are considered cleaner compared to chemical-intensive methods. For companies looking to reduce hazardous waste or meet green manufacturing standards, these can be strong choices.
In essence, the right method boils down to the specific needs of your application. Often, companies use a combination of techniques across different product lines.
Innovations in PVD and Vacuum Coating Technologies
Both PVD and vacuum coating have come a long way. Innovations continue to emerge, pushing the boundaries of what these technologies can achieve.
1. Multi-Layer and Gradient Coatings
Modern systems now allow for layering different materials in the same process. This enables unique material properties like a hard outer layer and a ductile inner layer for better performance.
2. Nanotechnology Integration
Coatings are now being engineered at the nano-scale. This allows for super-hydrophobic surfaces, anti-fingerprint coatings, and even self-cleaning finishes.
3. Plasma-Enhanced Processes
Adding plasma to the coating environment enhances energy efficiency and can improve adhesion and uniformity—especially in PVD and CVD processes.
4. Green Coating Technologies
Newer developments focus on reducing environmental impact. These include water-based cleaning systems, energy-efficient vacuum pumps, and non-toxic gas substitutes.
5. Real-Time Monitoring and AI Control
Advanced PVD and vacuum systems are now integrating AI-driven sensors to monitor deposition rate, temperature, and chamber pressure in real-time, making adjustments on the fly for optimal coating quality.
These innovations are reshaping manufacturing across industries—from aerospace to fashion. They’re making coatings more durable, customizable, and sustainable.
Future Outlook: Where Is This Technology Headed?
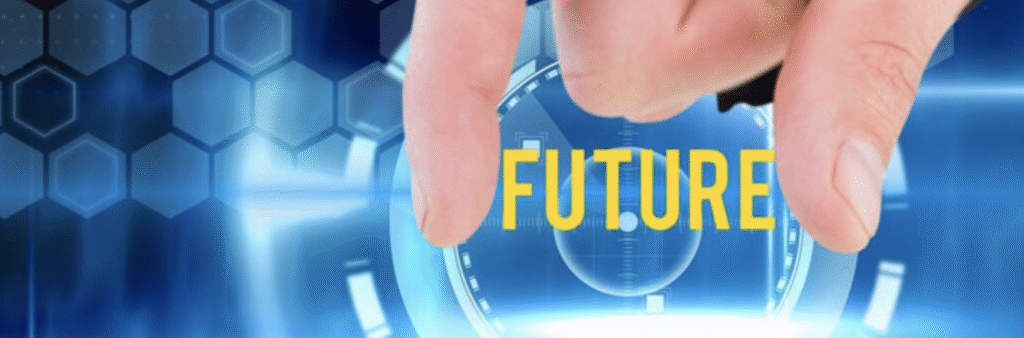
As industries become more demanding and environmentally conscious, the future of PVD and vacuum coating looks incredibly promising.
1. Wider Material Options
Scientists are experimenting with non-metallic compounds, including organic and composite materials, to create hybrid coatings for specific applications.
2. Portable and Scalable Systems
Imagine tabletop vacuum coaters for rapid prototyping or small-batch luxury items. Miniaturized, plug-and-play systems are already in development.
3. Coatings for Wearables and Smart Devices
With the rise of IoT and wearable tech, coatings that enhance durability, flexibility, and conductivity will be in high demand.
4. Mass Customization
Future systems may allow for rapid changes in coating composition or pattern—ideal for personalized goods like custom watches, phones, and automotive trims.
5. Eco-Friendly Regulations
Stricter environmental rules will push manufacturers toward greener, non-toxic coating methods. Expect even more emphasis on dry processes like PVD and cleaner gas chemistries in vacuum coating.
Whether you’re in design, manufacturing, or product development, staying on top of these trends will keep you ahead of the curve.
Conclusion
In a world that increasingly demands durability, efficiency, and aesthetics in everything from gadgets to industrial tools, PVD coating and vacuum coating stand at the forefront of innovation. They may sound similar—and they do share the vacuum environment—but they differ significantly in technique, application, and outcome.
PVD (Physical Vapor Deposition) is a subset of vacuum coating that relies on physical methods to deposit materials. It’s ideal for thin, hard, and decorative coatings with incredible adhesion and wear resistance. Its applications range from surgical instruments to luxury watches and high-performance cutting tools. The beauty of PVD lies in its balance between function and finish.
Vacuum coating, on the other hand, is a broader term encompassing multiple techniques including PVD, CVD, evaporation, and sputtering. It opens the door to more materials, processes, and use-cases, ranging from semiconductor manufacturing to solar panel fabrication and food packaging.
When deciding between the two, your choice should depend on the material to be coated, desired properties, production scale, and cost considerations. While both methods offer low environmental impact and excellent performance, each has its ideal niche.
The future of both technologies is glowing. With the integration of AI, nanotechnology, eco-friendly advancements, and customizable automation, both PVD and vacuum coating are set to revolutionize not just manufacturing, but how we design and experience products in our everyday lives.
If you’re in product design, R&D, or manufacturing, understanding the differences between these technologies is no longer optional—it’s a competitive advantage.
FAQs About PVD Coating Vs. Vacuum Coating
1. Is PVD coating the same as vacuum coating?
No, PVD is a type of vacuum coating. While all PVD coatings happen in a vacuum, not all vacuum coatings are PVD. Vacuum coating includes other methods like CVD, evaporation, and sputtering.
2. What industries use PVD coating the most?
PVD coating is widely used in industries like automotive, aerospace, medical, electronics, and luxury goods due to its durability and aesthetic appeal.
3. How long does a PVD coating last?
Depending on the environment and usage, PVD coatings can last several years. They’re highly resistant to corrosion and wear, which extends the lifespan of coated items.
4. Can PVD be applied to plastic or glass?
Yes, with proper surface preparation, PVD can be applied to non-metallic substrates like glass, ceramics, and some plastics, although care must be taken to avoid heat damage.
5. Is vacuum coating environmentally safe?
Generally, yes. Most vacuum coating processes are dry and do not produce hazardous byproducts, especially PVD and physical evaporation techniques. CVD may involve toxic gases, but newer technologies are addressing these concerns.