Mass Production: Factories and Processes
Mass production stands at the core of modern industrial efficiency. It enables manufacturers to produce large quantities of goods at scale while maintaining consistent quality and reducing costs per unit.
In this comprehensive article, we explore real-world factory examples, dissect the mass production process, and delve into the industries leveraging these systems for global supply and profit maximization.
Table of Contents
What Is Mass Production?
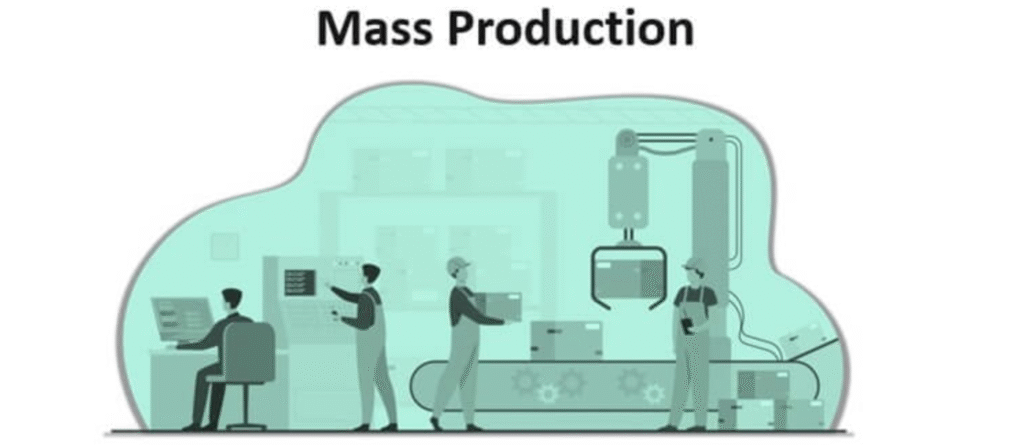
Mass production refers to the manufacturing of large quantities of standardized products, often using assembly lines or automated technology.
This method is widely used in industries such as automotive, electronics, apparel, food and beverages, and consumer goods.
At its core, mass production is about efficiency, scale, and uniformity. The model relies on:
- Specialized labor
- Automated machinery
- Repetitive processes
- Quality control checkpoints
Key Elements of the Mass Production Process
1. Standardized Design
Before production begins, companies develop a standardized product design to ensure every unit looks and performs the same. This uniformity is essential for maintaining product consistency across large volumes.
2. Division of Labor
Work is divided into small, specialized tasks handled by workers or machines. Each station performs a specific action repeatedly, increasing speed and reducing human error.
3. Assembly Line Automation
An automated assembly line enables parts to be added step-by-step, moving from one workstation to the next. Robotics and CNC machines often handle tasks such as welding, packaging, painting, and labeling.
4. Just-In-Time Inventory Management
Modern factories implement Just-In-Time (JIT) inventory to reduce waste. Components are delivered exactly when needed, which lowers storage costs and increases efficiency.
5. Quality Control Systems
Advanced quality assurance systems are integrated at every stage. These involve sensors, visual inspections, and sometimes AI-powered technology to detect defects in real-time.
Mass Production Factory Examples by Industry
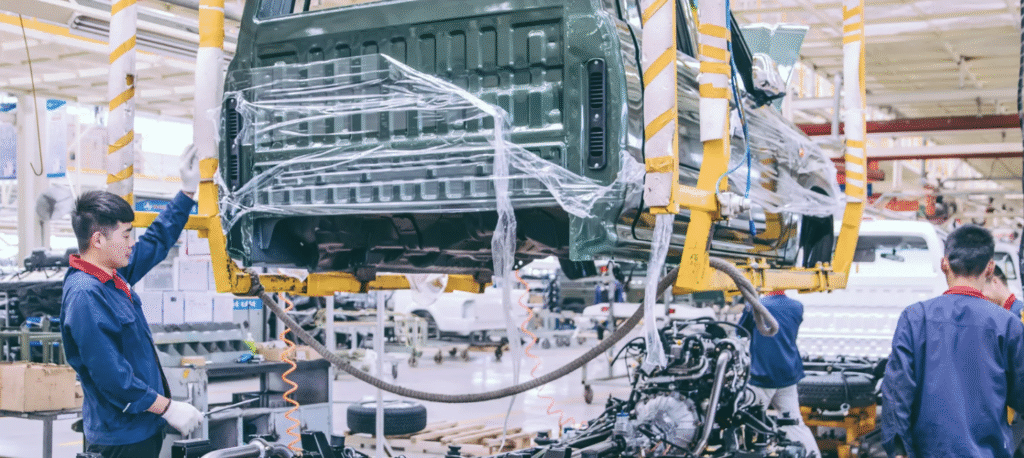
Automotive Industry: Toyota Production System
One of the best examples is the Toyota Motor Corporation. Their Toyota Production System (TPS) blends lean manufacturing with mass production principles. The system is renowned for:
- Kaizen (continuous improvement)
- Jidoka (automation with a human touch)
- Heijunka (production leveling)
Through TPS, Toyota produces millions of cars annually with remarkable precision and minimal waste.
Electronics: Foxconn (Apple Supplier)
Foxconn, based in Shenzhen, China, is the world’s largest contract electronics manufacturer. It mass-produces iPhones, iPads, and other gadgets for Apple. Key characteristics of Foxconn’s mass production system include:
- 24/7 robotic production lines
- High-speed SMT (Surface Mount Technology) lines
- Large-scale workforce integration
Foxconn’s factories can assemble over 500,000 smartphones per day, a feat only possible through refined mass production.
Apparel Industry: Shein’s Smart Factory System
Fast fashion giant Shein uses a unique on-demand mass production system, blending AI, data analytics, and agile factory networks. Key features:
- Micro-batch testing of designs
- Rapid scale-up for high-demand items
- Digital integration from concept to delivery
Shein can produce up to 10,000 new styles daily, thanks to its highly responsive and data-driven production model.
Food and Beverage: Nestlé
Nestlé operates over 400 factories globally, producing chocolate, coffee, dairy, and bottled water. Their production is highly automated, incorporating:
- Conveyor belt bottling and packaging
- Automated quality assurance
- Strict HACCP (Hazard Analysis and Critical Control Point) protocols
Factories can produce millions of units per day, maintaining the same taste and safety standards across borders.
Consumer Goods: Procter & Gamble (P&G)
P&G mass-produces products like Tide, Pampers, and Gillette using advanced robotics and logistics systems. Their factories include:
- Automated chemical mixing systems
- Real-time monitoring dashboards
- Cloud-connected machinery
This allows the company to serve over 5 billion consumers worldwide consistently.
Benefits of Mass Production
- Lower Cost per Unit: By producing at scale, the cost of labor, energy, and materials per product drops significantly.
- Consistent Quality: Standardized processes ensure each item meets the same specifications.
- High Output Volume: Factories can produce thousands to millions of units per day.
- Faster Time to Market: Streamlined production means products reach shelves faster.
- Efficient Use of Resources: Automation minimizes waste and maximizes material usage.
Challenges in Mass Production
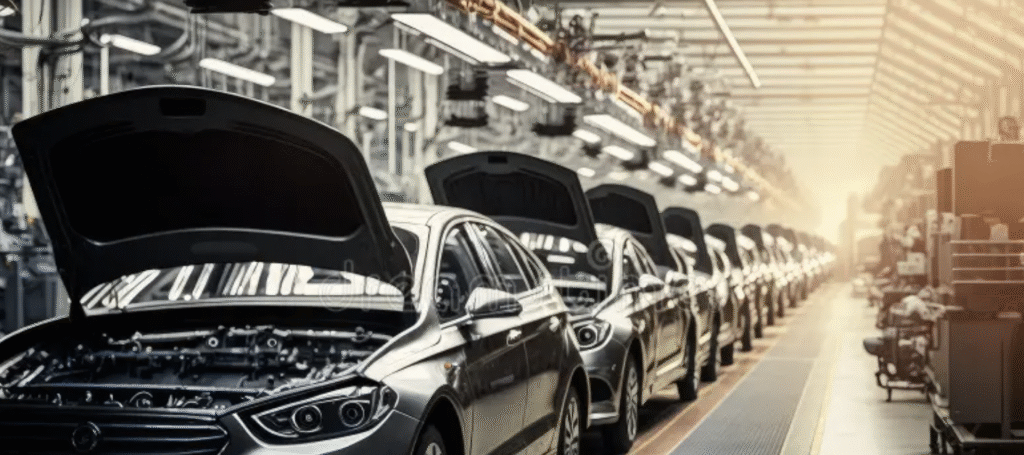
While mass production is powerful, it does face certain challenges:
- High Initial Capital Investment: Machinery, robotics, and facilities demand substantial upfront costs.
- Rigidity in Product Design: Once set, production lines are difficult to adapt for custom orders or new models.
- Environmental Concerns: High-volume manufacturing can increase emissions and waste if not managed properly.
- Workforce Monotony: Repetitive tasks can reduce job satisfaction and creativity among factory workers.
Sustainable Trends in Mass Production
Green Manufacturing
Modern factories are adopting eco-friendly practices, such as:
- Renewable energy sources
- Zero-waste manufacturing systems
- Recyclable and biodegradable packaging
Industry 4.0 Integration
The rise of Industry 4.0 brings smart technologies into mass production:
- IoT-enabled machinery for predictive maintenance
- AI-powered quality control
- Digital twins for virtual simulations and line optimization
Conclusion
Mass production has revolutionized how goods are made and delivered globally. From automotive giants like Toyota to tech behemoths like Apple and fast fashion leaders like Shein, this method enables global scalability with unmatched efficiency.
As innovation continues, expect the future of mass production to become smarter, greener, and even more adaptive to changing consumer demands.
Frequently Asked Questions (FAQs) About Mass Production
1. What is the definition of mass production?
Mass production is a manufacturing method that produces large quantities of standardized products using assembly lines, specialized labor, and automated systems. It is commonly used in industries such as automotive, electronics, and consumer goods.
2. What are some real examples of mass production?
Examples include:
- Toyota for cars
- Foxconn for electronics (like iPhones)
- Shein for fast fashion clothing
- Nestlé for food and beverages
- Procter & Gamble for household products
3. What are the key steps in the mass production process?
The typical steps include:
- Designing standardized products
- Dividing labor into repetitive tasks
- Automating assembly lines
- Managing inventory (often Just-in-Time)
- Conducting quality control checks
4. What are the advantages of mass production?
Mass production offers benefits like:
- Lower unit costs
- Consistent product quality
- High production speed
- Efficient use of resources
- Greater profitability at scale
5. What are the disadvantages of mass production?
Some drawbacks include:
- High setup and machinery costs
- Limited product customization
- Environmental concerns
- Worker dissatisfaction due to repetitive tasks